The number of shipping container manufacturers around the world continues to grow. Not for nothing, containers are important in facilitating the distribution of goods and supporting the needs of shipping goods or logistics. As the container industry advances, companies or businesses can now use various types of containers. Some examples are dry containers, high-cube containers, refrigerator containers, and insulated containers.
The use of containers can support environmental sustainability because of their high durability. In other words, you can use containers for up to 30 years. Environmentally friendly standards in the cargo industry are very important and companies must recognize them.
In addition, the container manufacturing process can be environmentally friendly, especially if it uses recycled materials. Environmentally friendly containers can help reduce the use of new materials, the impact of mining and processing raw materials, carbon footprints, and the risk of environmental pollution. Check out this article to learn how shipping container manufacturers make their products!
What Are Shipping Containers Made of?
Shipping containers must be incredibly durable. To protect their cargo, they must withstand extreme weather conditions at sea. Therefore, they need strong and unbreakable manufacturing ingredients, such as Corten steel.
Most components of a shipping container are corteen steel as it can be welded. The welding process allows for the creation of strong, durable structures that can withstand harsh outdoor environments, and it develops a protective rust layer.
Corten steel is a combination of steel and other metals. Although it might sound counterintuitive, Corten steel is deliberately made to rust. When elements are exposing a container, a thin layer of oxidization (i.e. rust) forms on the outer surface of the container. This creates an extra layer of protection on the container, which prevents further rust.
Shipping Container Manufacturing Process
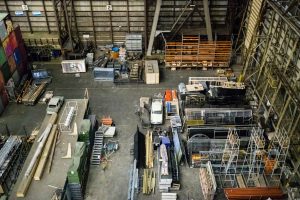
Step 1: Steel Coil Preparation
The shipping container manufacturers begin the process by unrolling and flattening the large steel coils to the desired thickness. These coils are high-quality steel with specific properties to meet industry standards.
Step 2: Cutting and Forming
In the next step, the flattened steel sheets are then cut into panels of precise dimensions of the container’s sides, roof, and floor. For this cutting process, you will need large hydraulic shears or laser-cutting machines. Also, you have to corrugate the shipping container to add strength to the walls and give the wave-like texture.
Step 3: Welding
This process utilizes welding techniques such as MIG (Metal Inert Gas) or TIG (Tungsten Inert Gas). The welding process aims to ensure strong and durable seams. Then, weld the panels together to form the basic structure of the container.
Step 4: Floor Assembly
The construction process of the container floor is different from its walls and roof. Its assembly primarily consists of two longer I-beams aid out perpendicular to each other. To create a slab-like base, weld smaller I-beams in between the longer I-beams. Once the welding is complete, sand the floor frame with a flap disc angle grinder to remove any rough welding joints.
Step 5: Surface Treatment
Do the surface treatment when the assembly of the container structure is finished. It aims to enhance durability and corrosion resistance. This process includes sandblasting to remove rust and contaminants, followed by priming and painting with marine-grade coatings.
Step 6: Door Installation
Install the container doors into the door frame openings. Then, add heavy-duty locking mechanisms to secure the doors during transit and storage.
Step 7: Priming and Painting
In the priming process, you can spray the container with the first layer of the paint. With this layer, the laborers ensure that the next coat sticks on the freight container and it also provides an extra layer of security from rust, corrosion, and other damages.
After priming, spray several layers of paint to ensure the maritime container doesn’t get affected by water, sea salt, heat, rain, and other elements for long.
Step 8: Decals and Identifications
After finishing the painting process, you can add your brand’s decals, logos, and labels with unique identification codes to identify the container. The identification code has 11 alphanumeric characters each of which corresponds to a meaning.
After labeling the container, the door handles and locking mechanism are attached. Then, wrap the rubber seal around the doors to make sure they are watertight.
Step 9: Quality Control and Testing
Throughout the manufacturing process, implement rigorous quality control measures to ensure that the containers meet industry standards and specifications. This may involve visual inspections, dimensional checks, and non-destructive testing methods such as ultrasonic testing.
To find out if there are any defects or leaks in the container, you can spray the container’s underside with a waterproof sealant. If there are none, the containers are complete and you can transport them to their intended location.
Finally, it undergoes a final inspection to verify compliance with relevant regulations and standards, such as those set by the International Organisation for Standardisation (ISO). Upon passing inspection, the container will get a certification for use in international shipping and transportation.
Components of a Shipping Container
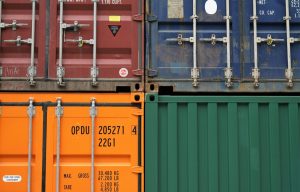
Despite their monolithic construction, containers are just assemblies of dozens of parts welded together into the steel boxes you’re familiar with. Most shipping containers have these unique features:
- Corner Castings: It is the reinforced corner posts of shipping containers that have openings for twist lock connections, allowing them to be connected to other containers or to anchor points.
- Twist Locks: It aims to securely connect shipping containers to anchor points or other containers.
- Cross Members: The space the cross members create between the ground and the flooring prevents moisture from seeping into the container from underneath. Cross members are one of the reasons that many container structures don’t require a foundation as it lifts the structures away from the ground and mitigates the risk of damage caused by natural elements.
- Forklift Pockets: It is the two openings along the bottom edge of the structures. Forklifts can insert the tines into the pockets to lift and move the structures.
- Cargo Doors: A storage container’s cargo doors are the two steel doors most often found at one end of the container. The cargo doors aim to prevent theft and weather intrusion on long voyages and offer formidable security for the assets contained within.
- CSC Plate: It indicates The International Convention for Safe Containers which aims to prevent structural failure and protect human life.
Conclusion
The use of shipping containers has been proven to facilitate the delivery of goods by sea or land. Therefore, it is not surprising that many shipping container manufacturers produce them because of the increasing demand.
To have a durable and strong shipping container, buy or rent from Tradecorp now! Standing at the top of the industry, Tradecorp is widely known for its high-quality containers open for so many creative applications. Fill out our quote form and we’ll guide you in finding the best container for your business goals!